Efficient Pallet Racking For Cold Storage
Posted on Sep 12, 2024
Amid Torrid Pace of Industrial Cold Storage Construction, Density of Racking, Equipment is Essential
You can hardly go a day without seeing news of plans for another industrial cold storage facility. The fast pace of cold storage construction is largely driven by consumer demands for frozen foods and kitted meals, and the continuing rise in online shopping – including shopping for groceries and cosmetics.
While developers are racing to construct new industrial cold storage facilities or expand existing ones, they face construction and operating costs that are significantly higher than common storage buildings – as much as three times higher. Those costs can’t be eliminated, but they can be controlled. That’s accomplished through highly efficient energy systems and building insulation, narrow aisles, adoption of automation for product placement and picking, and the type of pallet racking for cold storage that is selected. In a few cases, developers are building taller facilities to maximize cost-efficiency of the land and to minimize roof square footage and thus lessen heat loss.
A report on cold storage industry trends by Grand View Research anticipates a compounded annual growth rate of 17.5 percent between 2023 and 2030. The study notes the increasing reliance on automation in providing new levels of efficiency in refrigerated warehouses, and in reducing the need for labor, which typically can comprise about 50 percent of operating costs.
Opportunities to Update Older Industrial Cold Storage Facilities
While new industrial cold storage structures are being developed, the market also is served by plenty of existing facilities – many built long ago. The average age of industrial cold storage facilities is 37 years, notes Don Heemstra, vice president for sales and marketing at Steel King Industries. There is a real desire to modernize those facilities, installing pallet racking for cold storage that allows for narrower aisles and reduced load handling labor, and by engaging automation that allows the buildings to be as dense as possible.
The trend is to introduce or incorporate higher levels of automation, to maximize the utilization of the facility with automated storage and retrieval systems (ASRS). With the average pallet load weighing 2,500 to 3,000 pounds, crane-operated, unit load ASRS systems can play a role in efficient automated handling.
Depending on the clearance height of an existing facility, ASRS might not be the best choice. Long lead times and the prospect of raising the roof on a facility to justify ASRS might not be the best choice. Having an industrial cold storage facility unusable for six months is also an issue.
High-Density Industrial Cold Storage Is Essential
For industrial cold storage facilities, high density storage is a critical component. The cost to operate these facilities requires them to be full for the best return. Just like your freezer at home, you pay the same amount to operate it whether it has one item in it or it’s jammed full.
Semi-automated pallet shuttles are designed to drastically increase storage density for industrial cold storage facilities – while allowing for quicker positioning and retrieval of pallet loads and, consequently, reducing time that people need to be exposed to cold temperatures. While there are two-dimensional shuttles that can go down an aisle and then down a bay, one-dimensional shuttles that either go up or down a bay are more common. Both types provide your facility with important cold storage solutions by reducing the time an employee needs to be in the cold. All they need to do is place a pallet on a shuttle, and the shuttle positions it in the racking – or in reverse for retrieving pallets. These shuttle systems also reduce the risk of forklift-related damage to racking. Pallet Runner shuttles offered by Steel King effectively operate in temperatures as low as -22.
For industrial cold storage facilities where building cost are high and, thus, space optimization is crucial, high-density pallet storage becomes increasingly important in maximizing use of the cube. Drive-in racking, push-back racking, and pallet flow racking are examples of systems that allow for the storage of large quantities of pallets in a condensed footprint, while allowing time-saving access to pallet loads. When deciding which cold storage solutions are ideal for your facility, it’s best to consider these different types of pallet racking for cold storage that are available to you.
Drive-in racking is common in cooler and blast freezers, providing high-density industrial cold storage in a cost-effective manner. Pallets can be stored multiple positions deep, reducing the need for aisle space.
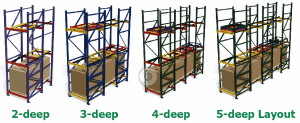
Pushback Pallet Racking
Push-back racking allows storage two to five positions deep. Pallets rest on nested carts which ride on inclined rails, allowing pallet loads to be easily pushed back, or removed as there is always a pallet at the aisle position. Like drive-in systems, push-back racking requires fewer aisles, but with these systems, each level can be independently accessed.
Pallet flow systems also rely on inclined rails, allowing loads placed on one end of the rack to move down to the unloading end. With loading on one side and unloading on the other, these systems allow for first in, first out inventory management, which can be important for industrial cold storage where food products are stored in cooler and freezer environments.
Greater density also can be realized by installing double-deep racking, which offers increased storage capacity while maintaining a high degree of selectivity. In these layouts, pallets are stored two-deep on single-sided units, or four-deep on double-sided designs. Steel King’s SK2000 and SK2500 closed-back tubular rack are ideal for use in double-deep and four-deep systems – with a design and materials that stand up to forklift abuse that is common with industrial cold storage environments.
All those pallet rack systems offer benefits in pallet racking for cold storage when compared to selective racking which, while being the most common form of racking, has just one pallet position. Thus, in selective racking, more aisle space is needed, so density is sacrificed.
Industrial cold storage facility operators need to determine which of the above systems best meets their needs and their financial models. In making those decisions, they also should consider the steel used to manufacture the racking systems – with structural steel recommended in pallet racking for cold storage. Structural steel, like that used in Steel King’s SK3000 Pallet Racking, provides greater overall strength and rigidity. That might result in a higher up-front cost, which can be offset by lower maintenance costs, increased load capacities, greater safety, and greater resistance to seismic forces in your industrial cold storage facility.
Whatever you need to handle when selecting your facility’s pallet racking for cold storage, contact Steel King to work with you in creating a solution customized to maximize use of every square foot of the facility.